Balancing vehicle performance with sustainability and efficiency
To meet growing consumer demand for ‘green’ but also wallet-friendly cars, automakers are deploying techniques to reduce vehicle weight and increase efficiency, says Saint Gobain’s Chris Needes.
The demand for reducing carbon emissions is a global issue that continues to grow in importance. Overall consumers globally have become more conscious of their finances and are demanding cars that cost less, produce less carbon dioxide (CO2) and aren’t going to eat into their disposable income by using excessive amounts of fuel. To meet these consumer demands, manufacturers are focused on deploying techniques to decrease the overall weight of the car and increase efficiency.
Small parts such as composite bearings and tolerance rings can make a big difference in optimising steering and powertrain systems to help achieve CO2 reduction targets. Composite bearings with a polytetrafluoroethylene (PTFE) liner are devices designed to negate friction between two moving parts, saving energy by facilitating movement. The consistent control friction offered by the engineering components with PTFE reduces wear and tear, contributing to the long life of the finished product with such components.
Tolerance rings are high-quality steel, radially sprung fasteners. The key feature of a tolerance ring is the protrusions or waves that run around its circumference, which effectively absorb vibrations, resulting in a noise-free driving experience. The tolerance rings’ waves can be customised in terms of the wave shape, height and harshness to ensure the optimal level of tolerance compensation and, thus, the perfect fit between two annular or ring-shaped components.
Improving automotive efficiency
In working to improve fuel efficiency, manufacturers must be careful to not jeopardise performance or safety and also consider the cost implications for the manufacturing process. Key to achieving this objective is the use of the ideal components for each application.
In looking at the exterior of a vehicle, manufacturers have started to evaluate the use of magnesium in place of steel in convertible car roof frames. However, using traditional steel-backed bearings in the pivots of a magnesium roof frame may leave the frame at risk of galvanic corrosion, where the more active metal corrodes preferentially to the more noble metal when immersed in an electrolyte, such as rain water. To prevent this, composite bearings backed with a metal of similar galvanic potential must be used. These lightweight, high-strength component alternatives not only extend the life of the roof, they also further reduce weight.
Additionally, reducing the weight of car doors is a focus, with aluminium door hinges increasingly used. However, aluminium is more susceptible to thermal expansion than traditional steel, which can affect the performance of the hinge. To circumvent this problem, steel-backed composite bearings have been developed with a larger outer diameter, creating a stronger press fit to compensate for the expansion of the housing. Improved tolerance compensation achieved through the tailored PTFE liner and material structure ensures consistently perfect fit between mating parts. In addition, aluminium-backed composite bearings can also be used to achieve the same thermal expansion levels as the aluminium housing.
Aluminium-backed composite bearings with the PTFE liner are corrosion- and wear resistant contributing to the long, maintenance-free life of the door hinge and enhancing quality perception of the car.
Manufacturers have also discovered new ways to reduce weight while offering the same performance values in the car interior. To achieve this, manufacturers are now using ultra-high strength steels instead of traditional materials in seat frames, which have enabled them to develop thinner, and therefore lighter, components that are able to bear the same loads as heavier designs. This has had an impact on the design of seat adjustors. The weight reduction in the seat frame has led to an increase in load on the adjustment pivots and on the bearing. To combat this, manufacturers have turned to higher quality composite bearings, which combine a thin design with a robust internal structure, to enable the component to withstand the extra loads created by a slimmer frame design. Thus, the use of innovative composite bearings allows car manufacturers to enhance the smart design of their vehicles with the use of fewer, lighter and smaller components.
We can also look at chassis design for examples of reducing weight in a cost-effective manner while improving safety and performance. Electric power steering systems have been adopted over the past decade to replace traditional hydraulic systems. These motors have traditionally been large and heavy to ensure high performance under high loads. However, more and more manufacturers are developing new smaller electric motors to help them meet weight reduction targets. To maintain the same comfortable, smooth steering experience offered by earlier larger motors, high-performing composite bearings with consistently low friction values are now being used at the interface between the motor and the rackshaft, enabling the smaller motors to turn the shaft as easily as larger models, while giving improved steering response and driver handling.
Thanks to advances in technology, powertrain components have been developed that support consumer weight requirements while offering improved NVH reduction, particularly with regard to the dual mass flywheel. The dual mass flywheel dampens torsional vibrations from the engine to prevent them reaching the gearbox, resulting in a more comfortable driving experience for the motorist, even at low revolutions per minute (rpm). The trend towards ‘downsizing’ engine components, such as reducing the number of cylinders, can actually increase the intensity of torsional vibrations. In order to combat this, manufacturers are now using composite bearings in the dual mass flywheel. The low friction values offered by the engineered components with the PTFE liner have led to NVH reduction compared with previous models and therefore contributed to noise-free mechanism performance. This in turn has enabled the development of smaller engines that reduce fuel consumption and CO2 emissions without sacrificing comfort for the driver.
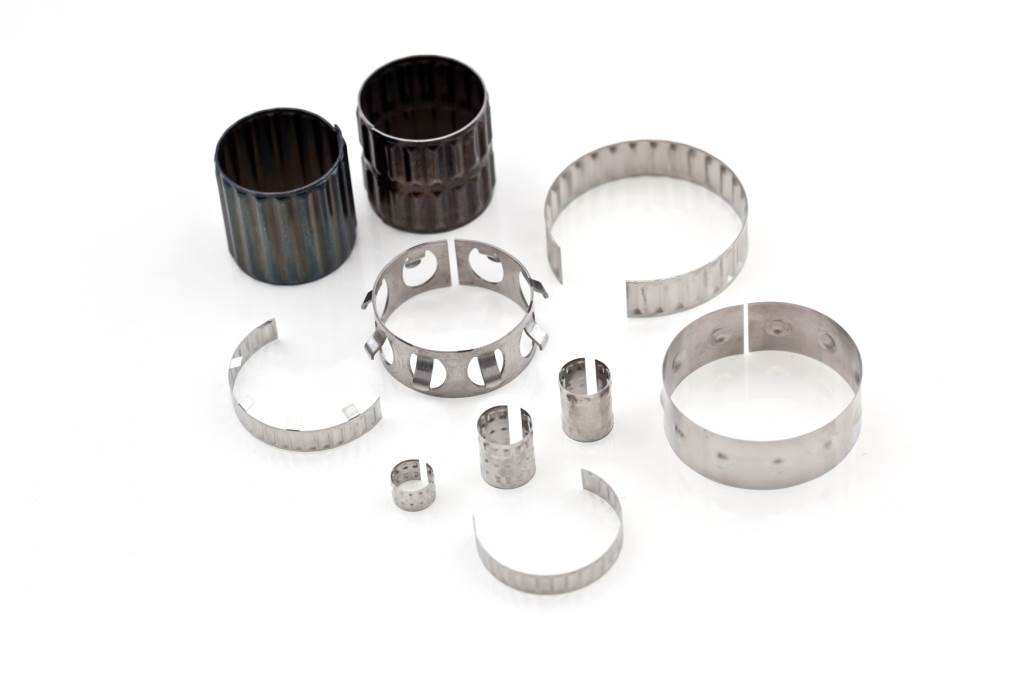
Moving forward
The market trends of recent years are clear and look set to continue well into the future. Rising oil prices and more stringent legislation regarding CO2 emissions are driving weight reduction and other energy saving innovations in the automotive industry. The demand globally is for high-quality vehicles that are affordable yet meet performance and safety demands. With innovative components, manufacturers can respond to these global trends without compromising on quality or cost.
About the author
Chris Needes is Global Market Manager, Automotive Chassis and Powertrain, NORGLIDE Bearings and RENCOL Tolerance Rings, Saint-Gobain.
RELATED ARTICLES
Branded content: HL Klemove inaugurates first Local ADAS Radar Manufacturing Unit in India, marks a significant achievement in “Make in India” initiative
The inauguration ceremony was held in the presence of Vinod Sahay, President and CPO of Mahindra & Mahindra Ltd. and Dr....
BluWheelz to 'Green Up' logistics sector
With their EVs-as-a-service solution, the startup is playing it smart with costs and looking to electrify the entire seg...
BRANDED CONTENT: Spearheading the EV revolution in India
Jio-bp is a joint venture between Reliance Industries and BP PLC where both entities have married international expertis...