Warren Harris: ‘EVs must be designed ground-up. Simply retrofitting existing car bodies with new batteries and parts won’t do.’
Insights into Tata’s strategy for green mobility, challenges in electric mobility, their association with Nio and much more.
Tata Technologies’ MD and CEO Warren Harris speaks on how the company's expertise can help OEMs utilise technologies for connected vehicles, hybrids and EVs; its 5R Rightweighting methodology that surpasses global standards of lightweighting with a multi-material production approach and advanced joining techniques, and on collaborating with start-ups on new-age technologies.
With the buzz around green mobility getting stronger by the day, how has Tata Technologies expanded its expertise for the automotive industry?
Green mobility is no longer just a buzzword – it is becoming more and more of a norm these days in a world which is looking to become increasingly greener, more connected and less manual. The industry has moved to make cars more efficient by leveraging technology that can effectively cut down emissions. Mobility is increasingly becoming more sustainable with regulations providing a solid backbone.
Attitudes towards emissions are changing with governments and industries globally working towards solutions to cut down emissions from combustion engines.
As a veteran organisation in providing engineering services for complete vehicle development and one of the leading engineering partners to OEMs, start-ups in the electric vehicles sector, Tata Technologies brings market-leading expertise to help manufacturers utilise technologies for connected, hybrid and EVs.
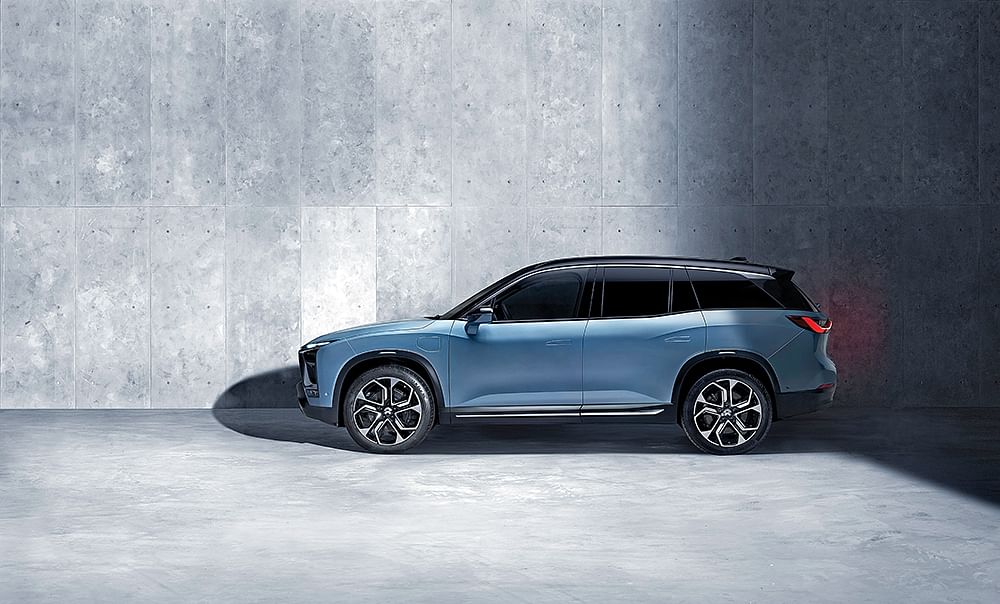
Tata Technologies’ experts and teams from China, India, UK and Romania worked with next-gen EV start-up NIO's engineering team to develop the ES8, NIO's first electric, all-aluminium vehicle.
Our intrinsic 5R Rightweighting methodology has proved to be imperative in surpassing international standards of lightweighting by using a multi-material production approach and advanced joining techniques. Our proven capabilities in mobility and telematics help organisations grow their business in these changing times. Understanding the need for a changed manufacturing approach, we combine the legacies of yesterday and smart solutions of tomorrow, harnessing the digital revolution. Our work with EV OEMs has been imperative in defining the agile landscape of this sector.
In 2017, you had mentioned that the share between captive and non-captive business was around 50/50. Recently, you announced the association with China’s NIO for complete production of the all-aluminium, electric ES8 sedan. What was the genesis of the project? How long did it take and what exactly was Tata Technologies’ contribution to the project across teams?
The association between Tata Technologies and NIO was initiated in mid-2015, very close to NIO’s inception as an ambitious next-gen EV startup. Since then, Tata Technologies has engaged with NIO to drive major engineering aspects related to the development of the ES8, such as body structures, closures and exteriors, advanced manufacturing engineering, PLM, and off-car connectivity.
Tata Technologies was able to pool in experts and teams from China, India, UK and Romania to work together with the NIO engineering team to deliver the final product which adhered to the highest standards in safety and finesse.
The first finished product – ES8 – is an all-aluminium SUV that broke lightweight index benchmarks and was delivered in record time from a blank page to a validation vehicle in world-class duration. Tata Technologies, in this strategic association with NIO, utilised its globally distributed execution model and extended its proven expertise in out-of-the-box engineering processes.
With the goal of creating a product-development process that would establish an industry benchmark, NIO and Tata Technologies have worked on a range of concepts on weight optimisation using advanced materials. The team has worked on creating a process that would pioneer the way for more advanced material-based vehicles in China. The result of implementing such expertise is that the ES8 is currently achieving Body Weight Efficiency targets better than the EuroCarBody Conference best.
The association has also achieved significant technological milestones in the PLM domain. The team successfully led and implemented the 3DEXPERIENCE 2016x (Dassault Systèmes) solution. It was delivered by Tata Technologies’ global talent and is another first in the next-gen EV Original Equipment Manufacturer (OEM) landscape, enabling engineers to accelerate the product development lifecycle through concurrent engineering.
For electric mobility to see mass adoption globally is a challenge of charging time and charging infrastructure. How do you see this being addressed in India and in developed markets?
The government of India has announced its intention of having an all-electric fleet by 2030, but many automakers and industry experts consider it an improbable goal. Part of the reason for this scepticism is the low demand for electric cars amongst consumers while the other part is the lack of the infrastructure necessary to create a flourishing industry. These challenges, however, can be addressed if we look at this challenge anew and learn from those countries where electric cars have succeeded. This includes China, the US, and some European countries.
Firstly, electric cars need a nationwide network of charging stations. In 2014, China’s State Grid announced its support for the development of privately-owned distributed energy organisations. This unprecedented move spurred investment in charging infrastructure by private companies and investors to the extent that China now aims to have 4.8 million charging stations by 2020, capable of meeting the needs of 5 million EVs.
The US has a different success story. The number of charging stations in the country increased dramatically between 2010 and 2016, as retailers and hotel owners installed charging stations to attract customers. More than a hundred metropolitan cities in the US have formed ‘Clean Cities Coalitions’ — non-profit public and private partnerships that promote a clean environment — and are encouraging the installation of more chargers.
Beijing has given priority to public transport vehicles and decided to electrify these before any others, while Paris is encouraging a bicycle share program, along with an electric car share program.
The government is doing its bit to promote EVs in India. It has launched schemes such as FAME (Faster Adoption and Manufacturing of Hybrid and Electric Vehicles) and NEMMP (National Electric Mobility Mission Plan) to support the development of the market. The state-owned Energy Efficiency Services (EESL) has invited global bids for 10,000 electric sedans and floated tenders for 4,000 charging points.
Electric cars must be designed from ground-up – simply retrofitting existing car bodies with new batteries and components won’t do. Newer, cheaper, more efficient batteries will have to be manufactured. But that shouldn’t be a problem as Indian engineers are possibly the best in the world when it comes to frugal innovation.
Do you think India with its own core competency of coming out with ‘jugaad’ will help OEMs develop a distinctive, low-cost-high-value proposition to address the emissions challenge?
Globally, more governments are becoming increasingly conscious of the pollution hazards caused by vehicle emissions. India has a history of monitoring emission levels and timely imposing norms on vehicles for better compliance standards. It is important that Indian OEMs also come up with timely, cost-effective solutions for dealing with the emissions challenge.
As a preferred engineering partner to automotive OEMs, Tata Technologies is aligned with the roadblocks ahead and has developed the right mix of strategy and solutions to make this transition smoother.
For Tata Technologies, what is the contribution from India in terms of the development of new technology and products in the global context?
Our Teardown and Benchmarking Lab in India, called the Axia-Vave Centre of Excellence, is our response to the growing global demand for frugal engineering services and our will to push the boundaries of innovation. With an 800 square metre space for teardown, our engineers carry out multiple projects in the lab to facilitate lightweighting, reverse engineering, cost analysis, competitive benchmarking, cost optimisation and product analysis services.
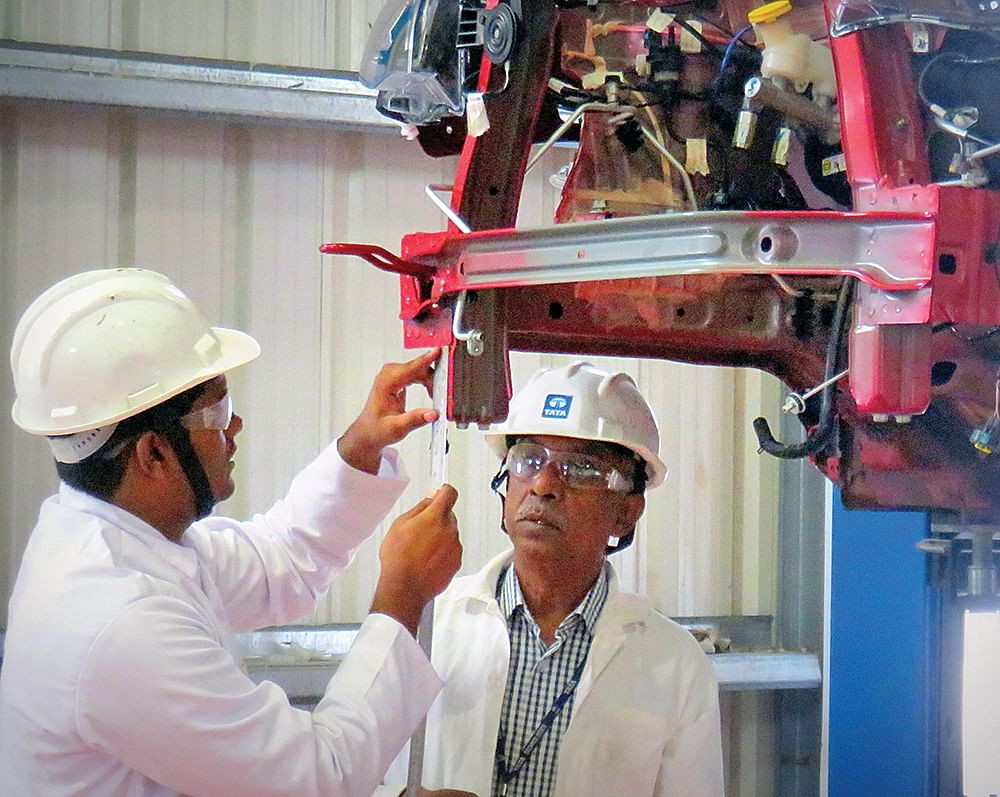
Tata Technologies R&D Lab — the Axia-VAVE Centre of Excellence — is where its engineers conduct multiple projects to facilitate lightweighting, reverse engineering, cost analysis, competitive benchmarking, cost optimisation and product analysis services.
Our expertise in technologies that redefine the manufacturing landscape digitally helps us to empower a company’s digital maturity journey. We have dedicated Centers of Excellence for new-age technologies such as Mobility, Big Data, Telematics, Cloud, Internet of Things (IoT) and Process Automation.
Tata Technologies has worked on projects for Indian auto clients in the fields of mobility, telematics and connected areas and provided them with an edge in this space.
Globally, there is an aggressive focus on digitisation from concept, design, shop floor to sales. How is this new opportunity presenting itself for you?
The world is increasingly moving towards digitally transformed products that interact with each other and their ecosystem. Our value proposition has two components – the first is outsourced engineering services that we deliver to automotive, industrial heavy machinery and aerospace manufacturing companies. The second is helping manufacturing companies create, curate and intelligently connect and use product and enterprise data to enhance their competitiveness in the markets they serve. We enable our clients to define and optimise better product development processes which help to return real value to their Product Lifecycle Management (PLM) strategy.
This marks an exciting phase for our organisation. As practitioners and advisors to leading manufacturing companies, we complement our services with a best-in-class understanding of digital engineering and Product Lifecycle Management providing the basis for effective program and product development execution. Our Connected Enterprise IT (CEIT) solutions help to digitally enable the entire manufacturing lifecycle, unlocking the full value of different process and applications that are part of the enterprise.
These services have placed us in the best possible position to ride this digital revolution. Compared to other engineering service providers, our services have given us the experience and the knowledge required to digitise the entire product lifecycle.
The automotive industry in its evolution towards electric, shared and connected mobility has seen a huge increase in the number of start-ups foraying into this space. How do you perceive this phenomenon and is this going to enable a level-playing field between legacy OEMs and the new entrants?
Automakers are increasingly collaborating with new-age start-ups to embrace the next big ideas. These collaborations represent a healthy synergy between the two: automakers gain access to new-age tech without having to reinvent the wheel.
Start-ups are playing a larger role in this industry – their innovation and passion, combined with an automaker’s experience, makes for an enriching partnership. The sector as a whole must secure its products across the entire supply chain by developing new ways to collaborate, create customer value and share growth opportunities.
Are you working with any Indian start-ups?
Tata Technologies has had a productive and long association with Indian start-ups and they form a critical part of our ecosystem. Currently, we are collaborating with automotive start-ups on new-age technologies.
The rise of connected vehicle technology will bring a huge thrust towards cybersecurity, thus opening up new avenues for technology and IT companies. What are the challenges and threats you foresee in this age of disruption?
While connectivity has the power to enrich societies, economies, industries, and companies, it is not without risks. Particularly in the automotive sector, cybersecurity threats are real, and for several basic reasons. There is a need to have a proper cyber-security framework with a specific set of controls.
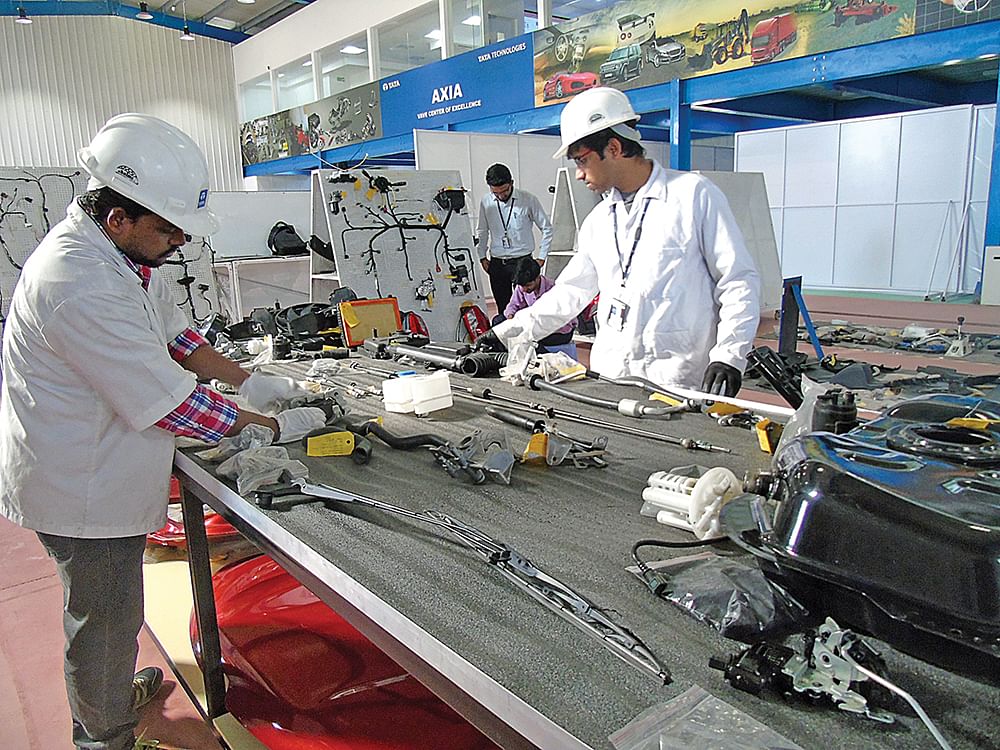
Tata Technologies R&D Lab - Axia-VAVE Centre of Excellence
OEMs are facing unique challenges given the increasing complexity of the product (for example, the large number of ECUs, lines of code, and level of connectivity), an extremely fragmented supply chain, and the integration of all these systems that can compromise any specific countermeasure. The solution in such a context comes only with a holistic approach that acts on two fronts. On the first front, specific cybersecurity solutions address the design of the product, how it is developed, and the maintenance and response architecture.
On the second front, OEMs must focus on the automotive environment at the industry level (to establish effective cooperation programs), with the regulatory bodies, and on the final users who are directly involved as active players in protecting their cars (for example, keeping software updated). In parallel, the approach should prioritise innovation, user experience, and product cost competitiveness at all times.
(This interview was originally featured in Autocar Professional's May 1, 2018 issue)
Also read:
NIO unveils six-seater electric SUV and a 1360hp electric supercar in Beijing
Tata Technologies and China's NIO develop all-aluminium electric car
RELATED ARTICLES
'India Can Become a Major Pillar for Us' - Marquardt Group
Björn Twiehaus, CEO of Marquardt Group, and Vishal Narvekar, the company's India GM, share their outlook on the Indian m...
Luxury Car Market to Slow in 2025: Mercedes-Benz Sees Flattish Numbers
In Jan to March of 2025, the market may witness its slowest growth since COVID-19, and if the weakness continues, the se...
‘We Must Have More Women Leaders in the Auto Sector:’ Anjali Rattan
The chairperson of the New Delhi-headquartered RattanIndia Enterprises believes that with their multi-tasking nature, wo...