SSAB keen to prove its mettle in AHSS
SSAB, an over-100-year-old steel company, started producing AHSS in 1978 in Sweden. The company, which is present in all key global markets like the US, South America, Europe and Asia including China, started its India operations in 2010.
Swedish automotive steel manufacturer sets up its India stock sourcing point in Bangalore in a bid to further accelerate local demand for its advanced high strength steel.
Changing industry regulations, the sharply increasing focus on safety and lighter vehicles have seen higher adoption of advanced high strength steel (AHSS) in vehicles across segments over the past few years. While the speed of adoption is more in developed markets, India's automakers are also taking to AHSS.
SSAB India is banking on these new trends by making available its AHSS in India. SSAB, an over-100-year-old steel company, started producing AHSS in 1978 in Sweden. The company, which is present in all key global markets like the US, South America, Europe and Asia including China, started its India operations in 2010.
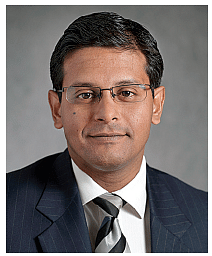
Speaking to Autocar Professional, Subhabrata Mukherjee, senior sales manager – Automotive, India, and Thailand, said, “We ventured into India because one of our global customers (Tier 1 supplier) needed our presence here to provide them with better service, establish the supply chain model and localise the product. So we followed our customer to the Indian market.”
Before its India entry, SSAB was supplying to its Indian customer from Sweden. Since then, being locally present, the company has developed a good customer base. While the India market was not ready for adoption of AHSS in the year of launch, there has been a gradual uptick in demand over the past seven years.
DEMAND GROWS FOR DOCOL
Since 2014, all key passenger vehicles – both in the premium and mass segment – have seen usage of SSAB’s ‘Docol’ automotive steel whose initial application for in seating applications and its components. Mukherjee says, “Besides seating systems, we also supply substantially for chassis and bumper applications in India. These are the three main applications where our AHSS is being used by vehicle manufacturers.”
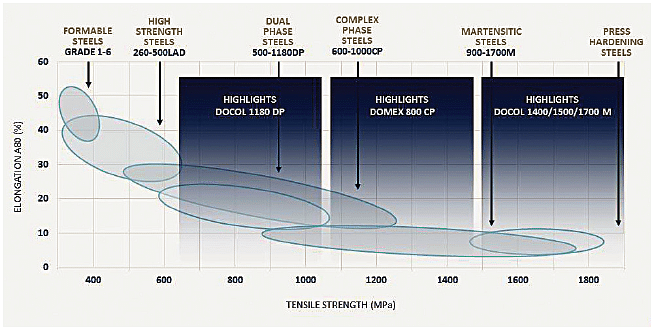
The Indian market has evolved over the past 3-4 years and most of the OEMs who use AHSS do so largely to drive gains in safety, lightweighting and driving performance. Also, new crash regulations, which are to be implemented in India, are compelling OEMs towards vehicle design that is safe and crashworthy. What is also helping SSAB is the consistently rising focus on achieving higher fuel efficiency levels as also reduced emissions in the form of the upcoming BS VI norms, which will see automakers develop lighter but stronger vehicles. AHSS is said to be a major enabler for the recycling of vehicles at the end of the life cycle.
SSAB says it works closely with its clientele in India. Usually, in the automotive industry, it takes considerable time before a material receives approval and takes even more time before the product comes into the market.
The company is also involved in a lot of training and information dissemination for customers about the right processes to use AHSS, be it at forming and/or design stage. It works together with the client's design and manufacturing teams to achieve the desired results in the end product. This approach has resulted into close coordination with a customer right from the early stage of product development and selection of the right material.
At present, the company supplies to all the major automotive OEMs and key global Tier 1 suppliers in India. “We have added 12-15 customers in the past few years, which has prompted us to start a stock point in Bangalore which we opened last year,” says Mukherjee.
The company imports all its AHSS from Sweden and supplies as per customer demand. Being logistically close to customers always makes a difference and as a result of the stock point in Bangalore, SSAB’s Indian arm is seeing its business grow rapidly. The company now supplies its steel to all the key auto hubs including Chennai, Bangalore, Pune and Delhi-NCR.
Speaking on the different types of steel for auto, Mukherjee said, “We can manufacture mild steel and ordinary steel grades. However, our main focus is in the niche segment which has advanced high strength steel starting from tensile strength 420-1700 Mpa.”
Given the heightened focus on safety, AHSS is widely used in automotive applications related to the body in white (BIW) structural components. The major five applications where AHSS is used include seat mechanisms, bumpers, structural components in BIW, side impact beam/ door intrusion beam and chassis. Globally, SSAB’s automotive team focuses only on the passenger car segment and buses. In India, the company primarily caters to the passenger car market.
BETTING BIG ON INDIA
Globally SSAB is focusing more on newer applications including electric vehicles and the company is targeting doubling of its turnover in the next few years. To achieve this goal, India is going to be a key market for SSAB. Now with its stocking base in Bangalore, the company is looking higher engagement with the automotive industry. “With one warehouse in Bangalore last year, we continue to follow our customers and will support them with our technical service, supply chain and knowledge of AHSS steels,” says Mukherjee.
The company, which aims to treble the Indian business in volume and sales turnover by 2020, plans to sell AHSS niche grades for automotive applications. The company is already working on several new projects and is confident about achieving this ambitious goal. At present, the company caters to seats, bumpers and chassis. With upcoming new crash regulations, it hopes to include the side impact beam and reinforcement/ rocker panel and other structural components soon in its applications list for India.
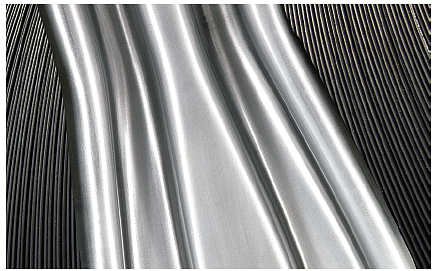
AHSS offers benefits like higher strength, safety and lightweighting but also commands a premium versus regular steel. But Mukherjee says putting a price for steel is difficult because the steel is used for making a final component. Value addition to steel happens at every stage. AHSS also helps in saving cost by making the vehicle lightweight which in turn improves both fuel efficiency and driving performance.
Martensitic steel can contribute up to 30 percent weight reduction in a component and other grades like dual phase, complex phase help reduce weight up to 10-20 percent, depending on the design, application and manufacturing process. In India currently, the company is not started selling martensitic steel, which is the most premium steel in the SSAB product basket. However, some OEMs are considering martensitic steel in their design which will come into the market due to increased crash requirements in a couple of years from now.
AHSS steel is relevant for EVs too where applications like battery protector and tunnel reinforcement, which uses roll formed profiles, are being used in such vehicles in the US.
With safety consciousness to the fore in India – and also globally – SSAB is bullish about the market here and the promise of speedier growth. Which is why it is all too keen to prove its mettle in this part of the world.
5 Myths (and 5 truths) about AHSS
New, exotic materials for future vehicles continue to be developed but SSAB says when it comes to cost efficiency, environmental impact and value for money, nothing can compete with advanced high-strength steel (AHSS). Here’s how the company debunks some of the top myths and highlighting the benefits.
Myth #1: Advanced high-strength steel grades are difficult to cut.
With the right tooling parameters and tool steel with sufficient hardness, ductility and wear resistance, you can obtain the sharpness needed for clean edge-cuts. And adjusting the clearance appropriately based on strength and thickness will reduce burr height.
Myth #2: Advanced high-strength steel grades are difficult to shape.
Harder than mild steel, that’s true. But if the designer has advanced high-strength steel in mind when designing a new car, modern steel grades can be formed into quite advanced products. Most important is calculating with the springback and the lower deep drawing capacity when using advanced high-strength steel. This means that the tools must bend the plate a bit more compared to mild steel. But when the angle is correct, the final product has all the advantages that come with the better steel, like lower weight, increased strength or both.
Myth #3: You can’t protect advanced high-strength steel from rust.
When on the road, a vehicle is exposed to a very aggressive environment. Winter conditions can be awful, with a mix of salt, sand and grit covering the bottom of the car. This used to be a big problem, but not anymore. By extensive use of hot dip or electrogalvanizing techniques, advanced high-strength steel can be delivered with different protective layers that efficiently prevent corrosion.
Myth #4: Joining and welding are complicated.
It is just as easy to weld AHSS as mild steel grades. In some cases, it can be wise to consider welding in other areas, but in general traditional spot welding and laser welding make very good methods for joining these kinds of steel grades. The welding parameters will require only minor adjustments. Compared with steel parts made by hot stamping, the process window for welding is wider when you use cold formable high-strength steel.
Myth #5: Hydrogen embrittlement must be considered using AHSS
This could be true from a theoretical point of view, but Docol 1400 M from SSAB and other high-end products made of advanced high-strength steel have been tested and approved by car manufacturers around the world.
(This article was first published in the August 1, 2017 print edition of Autocar Professional)
RELATED ARTICLES
Magnets of Disruption: How China’s Grip on Rare Earths Is Stalling India’s EV Dreams
As China tightens its grip on rare earth exports, Indian automakers risk delayed launches, disrupted festive season prod...
HYUNDAI CRETA EV: Off to a Slow Start
Hyundai has priced the electric version of its massively popular SUV close to the Rs 20 lakh range, where it has been fo...
Ashok Leyland Aligns Sustainability Goals With Business Operations
Ashok Leyland is embedding sustainability deep into its operational strategy, leveraging green finance, electrification,...