KCTR Varsha Auto bets big on sealed ball joint technology
Indo-Korean JV foresees potential in CV industry for innovative sealed ball joint technology, which calls for fewer child parts and reduces need for regular servicing.
KCTR Varsha Automotive (KVAPL), an equal joint venture between Korea’s T&G (Korea Central Corporation of Korea) and Varsha Forgings, is upbeat about its innovative sealed ball joint technology, typically for its applications in the commercial vehicles.
According to the company, it has introduced a unique ball joint technology that is used in tie rods and drag link assemblies, and involves fewer child parts as compared to conventional ball joints, thereby reducing the need for maintenance.
Talking to Autocar Professional, Yash Munot, managing director, KVAPL, explains that “the conventional technology uses serviceable or grease-able ball joints. These may fail prematurely while the vehicle is on the field due to a variety of reasons including regular wear and tear. The turning and driving on rough roads generates constant friction between the ball stud and the bearing parts. Rougher the road and more frequent the turns, the faster will be the rate of wear and tear. In Indian road conditions, this wear pattern is predominant and frequency of change of these ball joints not only eats into the vehicle's turnaround time but also affects the economics of several operators currently. Hence, a number of OEMs of commercial vehicles are opting for sealed-for-life ball joint technology. We are offering this technology after an extensive study and comprehensive research. This would be a major growth driver for us.”
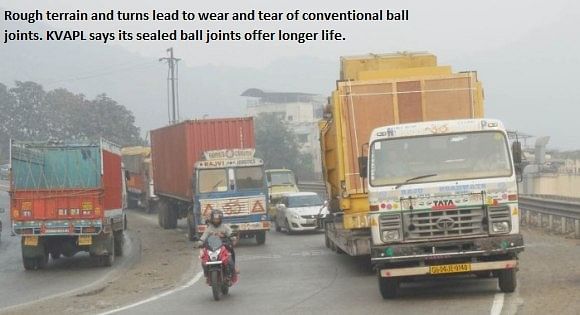
Multiple benefits
According to the company, this innovative ball joint technology offers multiple advantages over its conventional counterparts such as low friction between ball stud and the specially developed material (rubber seat). This gives high performance, high static and dynamic load capabilities, simple internal structure leading to fewer child parts, which makes it lighter in weight and a noise-free joint, high quality thermos polyurethane dust cover for longer life, and the use of progressive polymer technology parts results in lower preload on the ball joint assembly.
The company manufactures and supplies a range of steering linkages such as drag links, tie rods and ball joint assemblies for commercial vehicles. KVAPL’s current annual production capacity stands at 120,000 units of the drag link and 300,000 units of the ball joints.
“In case of increasing requirements that may come from additional infrastructure projects from the government such as coal mining activities, smart city projects, building new stretch of roads and others, we have the capability to boost our annual production capacities as per the demand. In the near future, we plan to augment our CNC machining facility, SPMs and the work force,” adds Munot.
Revealing his company’s order book, he remarks, “The company is working upon a handful of orders from commercial vehicle manufacturers such as Tata Motors, Hendrickson and others. We have approached all the major OEMs to update them about our new sealed ball joint technology. We are working on as many as 30 next-generation vehicle platforms of Tata Motors and hope to derive benefits when series production of these platforms goes on the floor. Similarly, the development with other OEMs is in the process of validation.”
While the company is optimistic about the foreseeable opportunities, the official says, it used its time well when the commercial vehicle market was low on demand.
“The recessionary phase was put to good use. Our products are proprietary parts and need a validation cycle of six months. We used this period to complete the test requirement of vehicle manufacturers and validate the products,” recalls Munot.
The company, which started its operations in 2014, is looking to establish its presence in the commercial vehicle market through technologically superior products. It is also focussing on the development of ball joints for tractor and SUVs.
Industry recognition has also come its way. KVAPL was awarded a gold trophy in ‘Excellence in Manufacturing’ for the year 2015 by ACMA. Commenting on this award, Munot says, “This was made possible due to the robust systems followed by our team. We have also acquired TS 16949 Certification in June 2015. We always have passion for excellence and continuous improvement.”
Q&A with Yash Munot, managing director, KVAPL
What is the level of the company’s investment since its inception?
KCTR Varsha Automotive (KVAPL) was formed as an equal joint venture with T&G (Korea Central Corporation of Korea) and Varsha Forgings in 2012. It manufactures steering linkages such as drag links, tie rods, ball joints and chassis-suspension parts. The design and technology is developed in Korea and enables KVAPL to provide high performance and maintenance-free components for automotive and agricultural applications.
Similarly, the JV partner Varsha Forgings (VFL) is a leading manufacturer of precision automotive components since 1986. As a forward integration player, VFL established a chassis and suspension parts division in 2007 for manufacturing components such as the torque rods and V-links for the commercial vehicles.
KVAPL has invested over Rs 100 million (Rs 10 crore) since its inception in the plant, machinery, and the infrastructure.
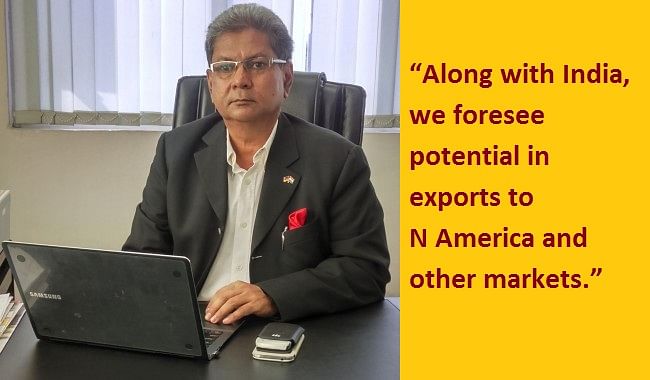
How has Varsha Forgings benefited with the JV with South Korea’s KCTR? What does this partnership bring to the table?
For Varsha Forgings, it is the forward integration with use of forgings as inputs for proprietary parts like drag links, tie rods and others. In fact the mission at VFL is to become one-stop solution for OEM’s steering linkages and suspension part requirements.
The KCTR brand is synonymous with high quality steering and suspension parts in South Korea. T&G (formerly Korea Central Corporation) is pioneer in manufacturing of suspension and steering linkages (drag links, tie rods, ball joint assemblies) for commercial vehicles and SUVs. They have 21 technology patents. KCTR is also a single source for these parts to Hyundai, Kia Motors, Isuzu, Tata Daewoo, and Mahindra Ssangyong in Korea.
KVAPL will harness the benefits of technology from T&G to offer world-class quality products to Indian commercial vehicle manufacturers. Both companies have a common mindset of customer-centric approach, satisfaction and quality.
We believe that KVAPL’s focus will be to capture sizeable market share of Indian OEMs — predominantly CV makers — and expand itself further to address the global business opportunities. Global players like Daimler India Commercial Vehicles, Scania and Volvo Trucks have started using India as a sourcing hub for their respective global requirements.
We also foresee great potential to export to North America, Ukraine, Japan and other lucrative foreign shores.
RELATED ARTICLES
Auto Giants Explore Hybrid Strategy as EVs Hit Speed Bumps
Slower-than-expected EV adoption, tight CAFE norms and ever-present efficiency demands are giving hybrids a second wind ...
Continental Taps India as Global Hub for R&D and Manufacturing
Continental’s spin-off of its automotive business into AUMOVIO marks a strategic shift, placing India’s engineering and ...
India's EV Story: Promise, Progress, and Challenges
Amid the fanfare of new launches and soaring expectations, mainstream buyers remain hesitant.