DSM Engineering’s metal-replacing plastics key to its future growth
DSM’s lightweight materials are widely used by the automotive industry. Some critical components wherein DSM materials are applied include under-the-bonnet parts like air intake manifolds, hot / cold side ducts, engine covers; structural parts like oil sump; aesthetic parts like door handles, mirror frames, roof rails; in auto electronics for connectors, sensors, actuator gears and also as insulation for cables used under a high temperature environment.
Advanced engineering thermoplastics are weight-reducing enablers and DSM is now exploring replacing the metal parts for EPS, among many other applications.
Stricter laws calling for a steep cut in carbon emissions and ever-increasing pressure to improve fuel economy are the two primary driving forces behind the fast-evolving lightweighting technologies in the global automotive industry. As a result, while on one hand, automakers have been exploring new metals and alloys to replace steel, which studies say account for about 60 percent in the making of an average vehicle (more in India), material specialists such as DSM Engineering are stepping in with thermoplastics to help OEMs achieve their lightweighting targets.
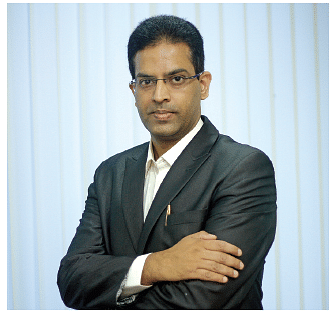
According to Anand Diwanji, business director, engineering plastics division, DSM India, meeting BS VI emission norms by 2020 is the major force driving weight reduction across all major automakers in India.
Throwing light in this context, he says, “The overall intention is to lower fuel emissions and to achieve a reduced carbon footprint. One of the ways to achieve this is via metal replacement. Our advanced thermoplastics are addressing this need. By replacing the uneconomical and un-ecological materials with tough, durable and sustainable thermoplastics, DSM enables lighter vehicles with lower fuel emissions and a reduced carbon footprint, and all at the most competitive system cost possible.”
According to the company, Akulon (PA6), DSM’s patented family of high performance polyamide 6 and polyamide 66 materials, is a proven and safe solution for airbag containers for over 20 years now. “A metal airbag container from 10 years ago contained 20 working parts, weighing 3.2kg. Today, we can make a container with five working parts, weighing as little as 1.0kg. Another example is the oil sump made using our impact modified and high-flow Akulon PA6, which reduces weight versus the traditional metal design by almost 40 percent,” underlines Diwanji, explaining its applications and benefits.
The senior official also reveals that the company is now exploring replacement of metal parts for the electric power steering (EPS) system. “Replacing metals in EPS (electric power steering) systems is one of the next steps we are taking. Recently DSM launched ForTii Ace, an important step forward into metal replacement territory, enabling OEMs to replace metals in applications that have been very challenging so far. ForTii Ace combines high and linear mechanical performance up to 150deg C with excellent chemical resistance.”
DSM launched ForTii Ace, a patented polyphthalamide (PPA) based on 4T chemistry, in October last year. The next-generation, high-performance polyamide, as the company claims, offers outstanding set of mechanical, thermal and chemical properties, which can be leveraged for multiple useful applications in the automotive and other industries.
Precisely, the company is looking at the die-cast metal replacement territory with the new material and the target areas include powertrain, transmission, chassis and thermal management applications.
A company document states, “automotive OEMs are expected to take around 200kg on average out of every car they make by 2025, in order to meet increasingly stringent CO2 emission norms in major automotive markets around the world. Engine downsizing, designing with limited design space, without compromising on safety and comfort are the core design challenges. Going ahead, ForTii Ace will have an important role in helping OEMs and their component and systems suppliers meet these CO2 targets.”
DSM’s lightweight materials are widely used by the automotive industry. Some critical components wherein DSM materials are applied include under-the-bonnet parts like air intake manifolds, hot / cold side ducts, engine covers; structural parts like oil sump; aesthetic parts like door handles, mirror frames, roof rails; in auto electronics for connectors, sensors, actuator gears and also as insulation for cables used under a high temperature environment.
“Yet another area where DSM innovations are benefitting OEMs and Tier 1 suppliers is friction reduction. Using DSM’s Stanyl in chain tensioners helps reduce CO2 emissions by upto1 gram/km. When used in gears for actuators, it reduces CO2 emissions by 0.06 gram/ km whilst reducing noise and increasing durability of these actuators,” adds Diwanji.
R&D IN INDIA FOR ENGINEERING PLASTICS
DSM opened its research and technology centre for engineering plastics in Ranjangaon last year (April 2016). The idea behind expanding local operations with a dedicated R&D setup was to not only grow business in India but also to support the local and global projects. The facility is to drive increased collaboration with customers in product development using a variety of equipment for material and application testing, including injection moulding, polymer characterisation, physical property testing and thermal analysis.
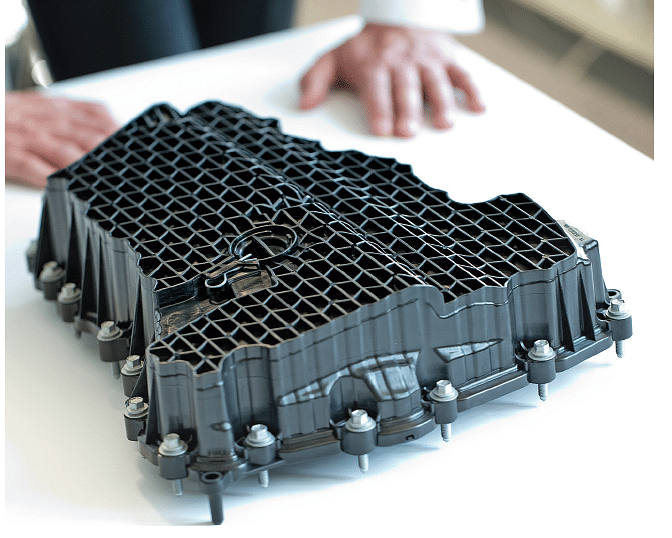
According to the company, the Akulon (GAXL) series is one innovative material developed at the India R&D centre. “We have developed Akulon (GAXL) series engineering plastics, which can be used with gas assist injection moulding giving excellent aesthetics and a solid UV performance of up to 3,000 hours in demanding external environments. This material is currently being used for unpainted door handles and mirror frames,” the senior company official reveals.
He adds, “The India R&D centre is heavily involved in global product and application developments. Additionally, we have plans to develop global competencies here (in Ranjangaon) in specific areas like long-term heat ageing and electrical application development.”
DSM, which has its head office in Netherlands, is betting big on India as a key market. This is aligned with its global corporate strategy of driving business in high growth economies.
Commenting on the future direction for DSM Engineering in India, Diwanji says, “The engineering plastics business has a world-class facility near Pune including a local R&D to cater to the needs of our global and local customers. In terms of our future direction, we have clearly identified the industry segments where we want to work and automotive is the most important amongst them. Our focus will be to support the OEMs in their lightweighting efforts by offering technologies either already available outside India or by developing solutions tailor-made for the Indian market. With this approach we aspire to grow above the average industry growth rate.”
He, however, refrained from disclosing the company’s financial performance in FY2016-17 and and the forecast for FY2017-18. “Business for DSM India (engineering plastics division) has been growing above the industry growth rate, especially so in the automotive segment. The same trend is forecasted for the current financial year,” he states.
DSM had invested in 2008 to build one of the largest greenfield engineering plastics compounding facilities in India. The unit, located in Ranjangaon, became operational in Q1, 2009 and since then has made impressive improvements in the area of sustainability (water reduction, energy reduction, waste reduction and renewable energy usage).
METAL REPLACING PLASTICS: A MEGATREND NOW
The global automotive sector is staring at several new technology mega-trends that are understood to transform the industry like never before.
While electric energy and hydrogen-based fuel cells are at the forefront of evolving new propulsion technologies, autonomous vehicles and shared mobility are bound to add a bulk of electronic content in vehicles.
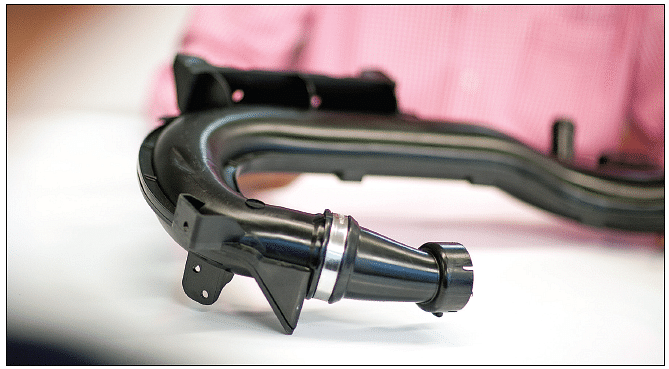
While automakers around the world are adjusting their operations to align them with these incoming mega-trends, component manufacturers appear to be at the helm of these fundamental changes. These changes will potentially force many to quit existing products and venture into new possibly more advanced counterparts for survival and growth.
For example, with the mechanical engine gone, the requirement for associated parts specifically supplied by DSM such as engine cover and oil sump may die out too. However, at the same time, the exit from one vertical will lead to entry into new opportunities.

Elaborating in this regard, Diwanji says, “The era of internal combustion engines as a single power source is coming to an end, indicating the transformation that makes vehicles cleaner. This transformation also signals new business opportunities, innovations and solutions. In the future, all individual parts of the vehicle, including under the hood, inside the car and exterior, will be connected via smart electronic devices, connectors and intelligent design. The new features of connected cars will drastically change the way people drive cars and will be as common as using mobile devices. The advanced technology in the automotive industry with the drastic innovations in electronics will begin to merge."
To accelerate these developments, OEMs and car manufacturers need new high-performance materials strong enough to withstand the extreme conditions they are faced with such as speed, changing weather conditions, high temperatures and others. In addition, the materials need to be designed to address the different characteristics of an electric car and make sure electric cars with big battery packs are safe.”
“DSM smartly combines the development of plastic by replacing steel to make cars lighter, withstand extreme temperatures and friction and enable miniaturisation by embedding an increasing volume of small electric circuits in the interior and exterior of vehicles,” he concludes.
(This article was first published in the October 1, 2017 print edition of Autocar Professional)
RELATED ARTICLES
Hybrids Gain Ground as India’s EV Transition Faces Infrastructure, Cost Hurdles
Slower-than-expected EV adoption, tight CAFE norms and ever-present efficiency demands are giving hybrids a second wind ...
Continental Taps India as Global Hub for R&D and Manufacturing
Continental’s spin-off of its automotive business into AUMOVIO marks a strategic shift, placing India’s engineering and ...
India's EV Story: Promise, Progress, and Challenges
Amid the fanfare of new launches and soaring expectations, mainstream buyers remain hesitant.