Seeing tomorrow today
Michigan's Detroit Engineered Products, whose CAE-driven design tools are helping automakers and suppliers improve and compress the product development cycle, is targeting India’s automotive industry for speedier growth.
The growing need for software and simulation products is drawing the world’s best providers in the field to India. Detroit Engineered Products (DEP), the Michigan-based global engineering solutions and services provider, which already has a footprint in this part of the world is one of them.
With India’s decision to leapfrog one generation of emission norms to upgrade directly to BS VI by 2020 and with OEMs looking to address the challenge of a faster product development cycle in one of the fastest growing automobile markets in the world, DEP is confident of achieving speedy growth.
Set up in 1998, DEP works with nearly all the leading automakers worldwide and has a presence in Japan, China, Europe and India. It is likely to expand its operations to Brazil soon.
With the rapid development in automotive engineering markets, there is a constant need to improve and at the same time compress the product development cycle. DEP says it provides effective solutions to automakers and suppliers by leveraging CAE-driven design at a very competitive cost. Its powerful tools – DEP Meshworks and CAD Morpher – have allowed various organisations to get a headway in product engineering and to explore various effective design options that may be available, in minimum time.
In a freewheeling discussion, Radha Krishnan, president, DEP, told Autocar Professional, “At present, we are serving automotive OEMs and suppliers in India, USA, Japan, Korea and Europe with the majority of our business coming from the automotive industry. We also work with other industries such as aerospace, off-highway and consumer goods.”
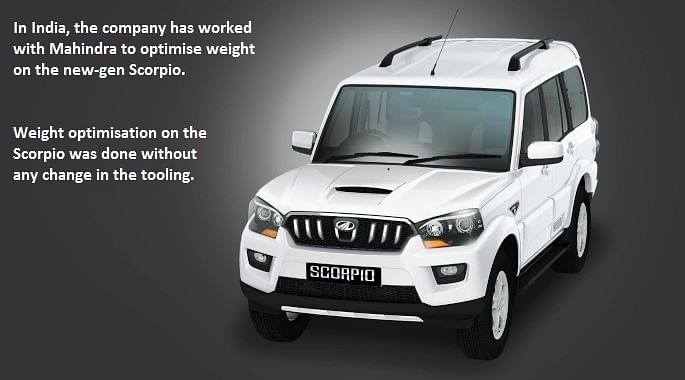
Typically, when OEMs start working on new vehicle programs before the actual prototype is developed, they have to design and prove in the virtual world. It is here that DEP helps with its solutions in virtual design and development that help cut down the cost of developing physical parts and also time to market.
Globally, DEP has been engaged with OEMs such as GM, Toyota, Nissan, Ford, Chrysler, Hyundai, Honda and suppliers like Delphi, Visteon, Magna, Borg Warner and American Axle helping them in virtual design and prototype.
DEP has CAE services which facilitate gains in the product-development cycle. They include:
- Crash (Non-linear transient dynamics)
- NVH (Noise, Vibration & Harshness)
- Stress, Durability & Fatigue
- CFD (Fluid Flow and Aerodynamics)
- Thermal and Combustion
- MBD (Multi-Body Dynamics)
- 1D (Systems Simulation)
- Morphing and Parameterisation
- Non-Parametric optimisation
- MDO (Multi-Disciplinary-Optimisation)
- Weight Optimisation
- Weld and Adhesive Optimisation
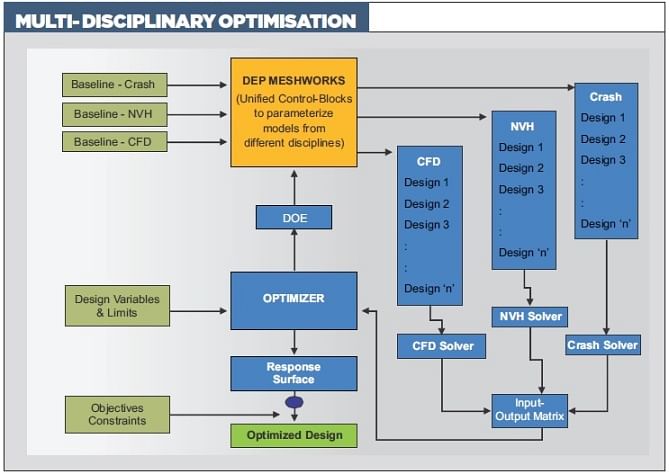
Elaborating on the company’s bandwidth for the automobile industry, Radha Krishnan says, “We are a product design and development company with our own products as well. We directly sell these products to OEMs. One of our major products is our engine sensor. Called the ‘in-cylinder combustion sensor’, it tells what is precisely going on with respect to emission parameters inside the cylinder, and it will be launched very soon. We have conducted a road show to display it to our Indian customers like Mahindra & Mahindra, Tata Motors, Bajaj Auto, Escorts, JCB, Sonalika, Cummins and Kirloskar Oil Engines,” says Krishnan.
DEP MeshWorks
DEP MeshWorks is a CAE-driven platform for rapid concept CAE and CAD model generation, parametrisation of CAE models, enabling optimisation, advanced meshing and CAD morphing. This software program was first launched in 2002 as an engineering platform and is now running with several updates.
Creating CAD data of a full vehicle can take anywhere from a few months to more than a year. However, DEP says with MeshWorks this time can be shortened dramatically by taking a previous-generation vehicle and quickly morphing it. OEMs see a lot of value in this as they have already spent a lot of time in design and development in the previous models. DEP’s morphing technology helps in reducing time, weight and meet all objectives for the vehicle. It also helps in improving aerodynamics performance.
“We are the first one to bring this morphing technology. A customer can take the CAD or CAE model data, quickly morph it and create a next-generation vehicle model faster. This adds significant value by way of reducing the design and development time and efforts,” says Krishnan.
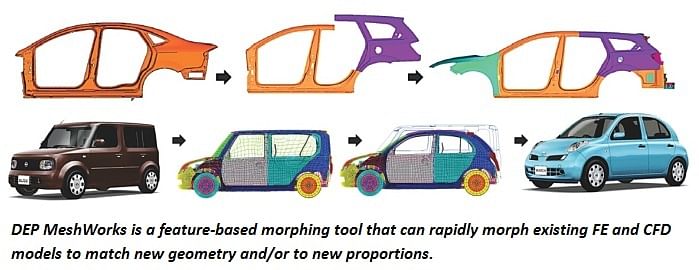
“General Motors, our first customer, has been using our software for the past 14 years. For every vehicle that it designs, GM uses our morphing technology for the first six months to morph old-generation models and analyse them for trying out different variations,” he says.
Similarly, Honda Cars uses DEP MeshWorks in Japan, USA, Thailand and Vietnam for its early design and developmental work. According to DEP, till date nearly 140 different vehicle programs globally have gone through this weight optimisation exercise.
In India, it has worked with Mahindra & Mahindra and helped it optimise weight on the new-generation Scorpio SUV without any change in the tooling. Similarly, in 2008, it had helped Tata Motors reduce 20kg from the Ace small commercial vehicle.
Engine of growth
DEP is also working on developing an advanced engine with primary emphasis on improving fuel economy significantly and reducing emissions substantially.
Like sensors, which will be manufactured by DEP, the advanced engine will be offered as a licensing technology to other OEMs after R&D, design, prototyping and field testing.
“As regards engines, we have different teams working on various areas all the way from packaging, manufacturing, intake system, noise and vibration, exhausting, rotating and reciprocating, components, thermal and cooling management, and ventilation within the engine,” says Krishnan. “What is unique about us is that we not only work with all conventional engines like common-rail direct injection or petrol engines, but we have an advanced engines group which works on new technologies which are to be brought out in the next 3-4 years,” he adds.
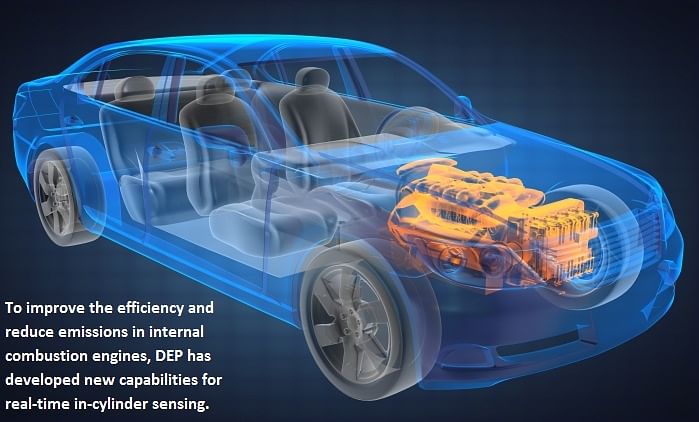
Three years ago, DEP participated in a joint engine program with Hyundai and Delphi in the US to design and develop a cylinder and engine block. The prototype engine, which powers a Hyundai Sonata in the US, has successfully demonstrated a 25-40 percent improvement in fuel economy and also better emission levels.
With manufacturing of sensors and engine design, DEP is investing heavily in manufacturing activities. In-cylinder sensors are a key enabler for advanced engines and DEP has been investing in that technology.
Over the past five years, DEP has participated in around 25-30 engine programs, all of which are now in production. It has also been working on a four- and six-cylinder engine for an American OEM and on a single-cylinder experimental engine for another customer.
Focus on India
Of the emerging markets, DEP has a sharp focus on India. It is keen to make the most of the opportunity that is emanating from the implementation of BS VI emission norms in India. The company believes its engine solutions and sensors, which play a key role in meeting BS VI criteria without the need for expensive after-treatment solutions, will click with automakers in India.
Considering the stiff timeline of 2020, it is felt that most OEMs are going to be stretched for the time if they have to change the engine design and their primary choice will be after-treatment solutions. To capitalise on this opportunity, DEP has a special team focusing on providing appropriate after-treatment solutions. DEP is investing in these advanced engines with the singular goal of taking these technologies to Indian OEMs or engine makers.
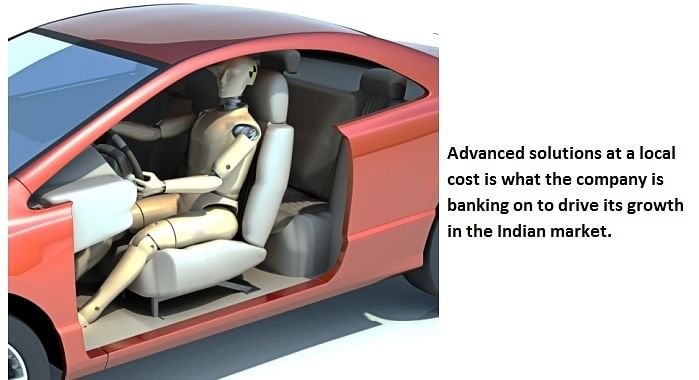
The company has a 150-strong team of engineers based in Chennai to provide services to local companies. While foreign carmakers like Ford, Hyundai, Chrysler and General Motors in India use DEP solutions in product development and design, DEP's local clientele includes Mahindra & Mahindra and Tata Motors. DEP's confidence in the Indian market stems from a cost-efficient package. “We are providing our customers in India all the advanced solutions at a local cost,” affirms Krishnan.
While DEP does face competition in the Indian market, it is banking on the user-friendliness of its software solutions to do the job right.
This feature was first published in Autocar Professional's October 1, 2016, Software & Simulation special issue.
RELATED ARTICLES
Digital Design Transforms India's Auto Sector
Auto makers leverage Modelling and Simulation (ModSim) to cut development cycles from five years to under two, reshaping...
Zen Mobility’s Micro Pod Aims to Bridge Last-Mile Delivery Gap
With modest sales, expansion plans, and bets on future tech, Zen Mobility has to focus on execution to ensure that its '...
The Design Strategy Behind Mahindra's Remarkable Rise
How Mahindra went from relying on global design houses to building a future-ready, digitally empowered, and globally cap...