‘Apollo is keen to go to the higher end of the motorcycle tyre segment.’
Apollo Tyres has diversified into the two-wheeler tyre market with its Acti range for motorcycles and scooters. P K Mohamed , Chief Advisor - R&D, speaks to Shobha Mathur on how the fully indigenous tyres were developed.
Apollo Tyres has entered the two-wheeler market with its Acti range of tyres for motorcycles and scooters. P K Mohamed, Chief Advisor - R&D, Apollo Tyres, speaks to Shobha Mathur on what went into developing the fully indigenous tyres.
Since Apollo’s two-wheeler tyres have been indigenously developed, how much of the development was undertaken at Chennai R&D centre?
We have a concept called customer-involved design. We made over 30 designs in different patterns and clinicked them to a group of customers, dealers, drivers, test drivers and fitters. Then we chose the pattern and evaluated it with respect to its performance.
Three parameters are very critical for the performance of a motorcycle tyre. Foremost is safety, then comfort and the third is mileage. The braking distance determines safety, cornering is also safety. So we identified 5-6 parameters and looked at our competitors’ design and how much it meets the requirements. We found a gap and converted that into our strength.
How different are the motorcycle tyre designs compared to the scooter tyres?
A motorcycle operates at high speed and leans heavily while a scooter will not lean heavily. Therefore, straight traction and leaning traction are very important aspects for motorcycle tyres. For scooters, they are not so important. Normally, a scooter tyre is designed for 100kph while an Indian motorcycle goes upto 150kph.
We have taken almost a year and a half for development and another six months for testing. We have a big R&D centre but an exclusive team of 10 people worked on it.
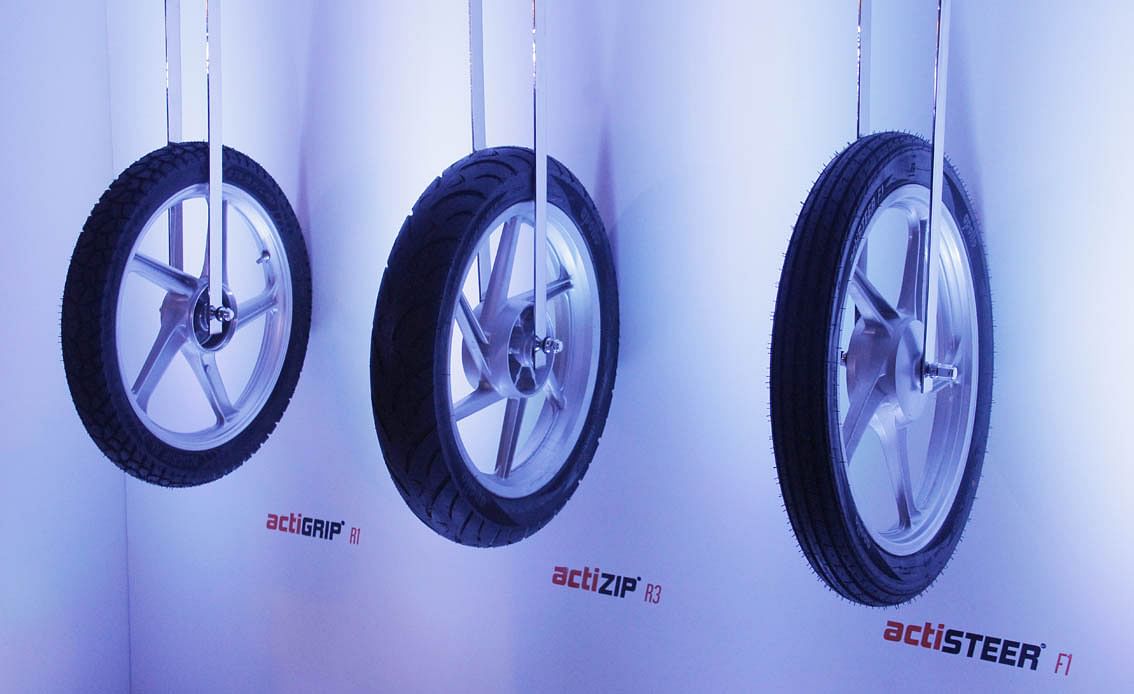
Did the Netherlands R&D centre also contribute towards the inputs?
The company is involved in making high-performance tyres. We make passenger car tyres up to high-speed W-rated tyres and have compounding and manufacturing technology to meet such a requirement. Motorcycles fall into that category and we have taken the inputs from the Netherlands R&D in the respect of the compounding technology. We have had to tune it.
Rubber has three stages – rubbery stage, leather stage and brittle stage. The brittle stage rubber will not give grip, which is also not there in the leather stage. So it our responsibility to maintain rubbery properties throughout all temperature ranges. Also, the rubber need not get hardened by ageing. If the hardness of the rubber changes, the grip will also change. We have taken all the factors into special consideration in undertaking our development.
Apollo plans to develop special two-wheeler tyres for the ASEAN and African markets. How different will they be from those made for India?
These tyres will also be developed in Chennai and the benchmarking has started. More traction is the most important parameter, the hydroplaning effect as well as wet traction. In India, dry traction is more important with very little wet traction. In Europe, wet traction and ice traction become more predominant and you need special compounding to meet such a requirement.
The tyres will not be sent overseas immediately as the Indian market itself has a requirement for 5-6 million tyres.
Compounding and design will be different for the tyres for the ASEAN and Africa markets. A more directional pattern will be more popular there than in India. In India, both designs are available and depending on the geography they can select the application and send a speed capability. In Africa, the speed is higher and so traction is the most important criteria for the tyre as motorcycles should not wobble. At high speeds, a 1mm wobble can create several folds of disturbance to the tyre; so comfort and traction are the most important parameters when you go overseas.
How much testing was undertaken for the two-wheeler tyres?
We used a five-time international winner for undertaking first-hand testing of the tyres. We selected 10- 15 vehicles and gave them to a professional agency which fitted the 100 percent indigenously designed tyres. Checks were conducted every 4,000km. We tested the tyres around 30,000 to 40,000km; the front tyre was tested across 60,000km while the rear tyre was tested over 40,000km.
What were the technologies leveraged in Chennai for the developmental work? Going forward, which will be the new technologies in demand?
We have a very elaborate R&D centre which houses a material categorisation laboratory, a design lab, a design simulation lab, a testing lab and a reverse engineering laboratory. This means we can analyse and find out 98 percent of the product. We also have a compounding laboratory which we use for the development of the material and simulation. Once you make the design, it can be simulated to see how it will perform.
Now radial is the new technology but in motorcycle tyres the focus is more on comfort and safety and these are the areas where technologies are moving. Radials are coming in motorcycles and not scooters.
Which segment will Apollo be working on next?
I think Apollo is keen to go to the higher end of the motorcycle tyre segment. At present, we have tyres for upto 150cc motorcycles; for scooters, the tyres are for 100cc models.
Have you started work on the higher-capacity tyres?
No, we are first launching these tyres but we will start work immediately to get into the Ducati and Harley-Davidson range. As I mentioned before, there are three aspects of a tyre – safety, comfort and mileage. Mileage and safety is a design parameter but comfort is a manufacturing parameter for ride and handling, wobbling, balancing, radial force and lateral force. We will be concentrating on all these aspects when we move to tyres for bigger bikes. More changes in the directional pattern will be necessary for higher-capacity bikes. When speed increases, the hydroplaning effect is more because water accumulation at the bottom of the tyre will be much higher than the water drainage. This means designing of the groove has to be such that there is no water film that makes a tyre skid. These are some of the minor things that we have to take care of.
RELATED ARTICLES
India: A Bastion Of Stability for Schaeffler
German autoparts maker Schaeffler’s CEO, Klaus Rosenfeld, describes India’s role in the company’s €24-25 billion empire....
'No Question of Us Being Late' - Suzuki India on e-2Wheeler Market
Suzuki Motorcycle India believes its EV entry is timely as the market is now mature enough to grow off genuine demand ra...
'India Can Become a Major Pillar for Us' - Marquardt Group
Björn Twiehaus, CEO of Marquardt Group, and Vishal Narvekar, the company's India GM, share their outlook on the Indian m...