Continental's new radial-axial turbo boosts Audi A3’s next-gen 2.0l TFSI
Developed by the global technology company Continental, the new gasoline turbocharger raises the bar with a substantial improvement in response, efficiency and robust design
The first Continental turbocharger with innovative RAAX turbine technology, now in production on the Audi A3’s new 2.0-litre turbocharged petrol engine (2.0l TFSI EA888, generation 3B), marks a new chapter in Continental’s successful turbocharger business. Significantly improved engine response is just one of the benefits of this new product.
“In the gasoline engine sector, in particular, global demand for turbochargers is set to rise sharply. We are very well positioned in this market, and at Audi we are delighted to have been able to win over an important customer with our innovative and robust solutions,” says Wolfgang Breuer, Head of Continental’s Engine Systems Business Unit, which includes the Turbocharger Product Line. “RAAX technology, now in production in a corporate engine platform on the Audi A3, will help us further strengthen our market position. Additional growth will also be generated by the new plants we are building in China and North America, which are due to start turbocharger production in 2017 and 2018 respectively.”
The new-generation engine is an example of Audi’s ‘rightsizing’ philosophy. This approach looks beyond downsizing and downspeeding, says Dr. Rainer Wurms, Head of Gasoline Engines Pre-Development at Audi AG: “Downsizing and downspeeding must also be precisely calibrated to vehicle class, engine power and real-world efficiency requirements. Rightsizing is about striking the right balance between these factors,” says Wurms. “An application-specific turbocharger is a key part of this approach. So we are delighted that, with close cooperation and support from our development partner Continental, we have found the perfect solution on this front.”
As denoted in the name RAAX (which stands for ‘radial-axial’), the new Continental turbocharger’s most important innovation is its modified turbine design. Unlike the most common type of gasoline turbochargers today, the radial turbocharger, which features a radial exhaust gas inlet, the new Continental turbocharger has a radial-axial (semi-radial/semi-axial) inlet path. The associated special blade design allows a substantial reduction of approximately 40 percent in the rotational moment of inertia of the turbine wheels. This means the turbocharger responds faster to engine load changes, so boost pressure is developed more quickly and turbo lag is minimized. In addition to this significant improvement in response, RAAX technology also results in up to 3 percent greater efficiency in the engine relevant operating range, leading to reduced emissions.
Robust and reliable
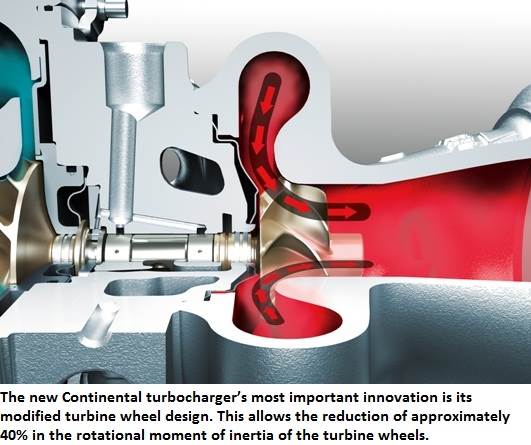
An innovative solution has also been implemented for the wastegate valve, which prevents boost pressure from rising too steeply at high engine output. Here the turbocharger team was able to leverage internal synergies because Continental’s existing technology portfolio already features an electronic wastegate control system noted for its high reliability. In the new turbocharger, the wastegate actuator system has been adapted to provide a very robust solution for the actuator/wastegate linkage.
Continental says robustness is further enhanced by a fully automated production system. Whereas conventional turbochargers have to be assembled in several stages, partly by hand, all the main components of the Continental turbocharger are designed for fully-automated, single-axis assembly. Using this production process, and intelligent quality control methods, Continental has raised the bar for quality in the turbocharger market.
“Our RAAX™ turbocharger sets the standards today for both thermodynamics and transient response,” says Udo Schwerdel, Head of Continental’s Turbocharger Product Line. “This is also coupled with robust design and high quality, which are always a top priority in our development projects. These high-quality standards are further underpinned by our standardized, state-of-the-art production methods, which we will be adopting at our new manufacturing sites too.” At present, Trutnov in the Czech Republic is Continental’s sole manufacturing site for the new turbocharger, but a further facility is already under construction in China. “From 2017, this plant will manufacture turbochargers for a number of volume production projects”, says Schwerdel. “Another facility is also under construction in North America. Production orders are already lined up for this new plant too, which is due to open in 2018.”
RELATED ARTICLES
Visteon opens high-tech automotive testing lab in Bulgaria
The facility, which is equipped with cutting-edge technology and houses over 70 highly skilled engineers, expands the co...
Honda to invest $11 billion in building EV value chain in Canada
In line with its plan to set up an environmentally responsible EV and battery plants in Ontario, the Honda EV value chai...
Audi opens its first EV charging hub outside Europe in Tokyo
The compact Audi charging hub has two charging stations with a total of four fast-charging points featuring CHAdeMO char...