IAC explores new innovative tech for maximum gains
IAC Group innovates with new eco-friendly concepts like Fibreframe and the HybridFleece moulding process in its quest to achieve gains in shedding weight. Amit Panday reports.
Luxembourg-based International Automotive Components (IAC) is among few global suppliers which are aggressively pursuing new technologies to achieve maximum weight reduction in the components it designs and manufactures.
Recently, IAC spotted the increasing popularity of sunroofs and panoramic roofs in passenger cars across segments, which, according to company officials, inspired its R&D team to develop new lightweight concepts.
Sharing the latest updates with Autocar Professional, PC Jayan, director of engineering, IAC, says: “We have developed stiff and lightweight concepts, which help realise different fixation concepts on the car body, the sunroof or the panoramic roof module. FiberFrame, an environmentally sustainable, lightweight and natural fibre sunroof frame was produced in November 2015 at IAC’s Centre of Excellence for overhead products in the Czech Republic. The product is first made for the new Mercedes-Benz E-Class to be launched in 2017."
Read more: IAC’s new Czech Republic plant starts production of lightweight acoustical solutions
According to Jayan, IAC’s FiberFrame replaces the sunroof’s metal reinforcement frame with a lighter frame employing strong, natural fibres using a new raw material comprised of 70 percent renewable content.
“This unique lightweight solution is reinforced using IAC’s EcoMat natural fibre-based semi-finished material, which was especially developed for this application. The fibre mat is moulded with a thermoset binder and is manufactured in-house by IAC in a hot moulding process. By manufacturing this product in-house in our headliner plant, we follow our strategy and expansion of vertical integration of our interior systems. Thanks to our global manufacturing footprint and standardised processes, we are now able to adapt the IAC FiberFrame to customer needs and supply it around the world,” explains Jayan.
The new product has high stiffness for improved structural rigidity and enables up to 50 percent in weight saving compared with conventional steel frames. Compared to conventional thermoplastic frames, he says, FiberFrame also prevents warpage after climate testing, and has shorter lead times than the conventional steel moulding tools.
Hybrid Fleece Moulding
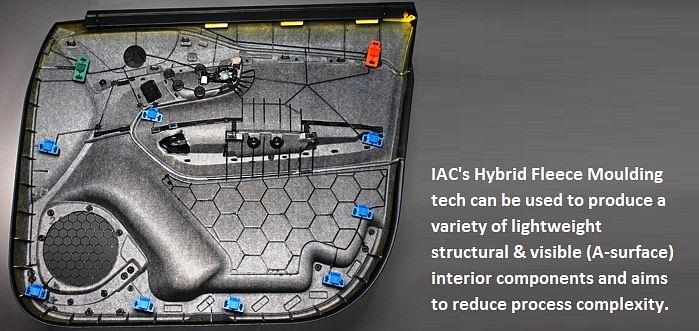
IAC has developed another innovative process patented as HybridFleece Moulding. This is a unique process for combining the pressing of a thermoplastic mixed fibre fleece from a natural fibre, glass or recycled carbon fibre with the moulding of stiffening ribs and clips into a one-step process in the same moulding tool with no need for additional welding or gluing.
The senior company official says that the process allows for significant weight savings in vehicle interiors. “The technology can be used to produce a variety of lightweight structural and visible (A-surface) interior components and is designed to reduce process complexity. In order to compare IAC HybridFleece Moulding with conventional processes, IAC produced a door carrier concept and tested it against the serial SUV product it delivers to an OEM customer. In the present case, the concept door carrier delivers a mass reduction of 35 percent and – with regard to its greenhouse potential – 40 percent less emissions over the course of its lifetime,” Jayan elaborates.
Lightweighting a global phenomenon
While studies highlight an alarming rise in the CO2 emissions globally, it is understood that over 90 percent of the world’s transportation energy is derived from burning fossil fuels. Although this trend has set off an inevitable quest exploring alternate fuel technologies, OEMs are aggressively pursuing weight reduction techniques to curb emissions and boost fuel economy.
Eco-friendly and lightweight FiberFrame is to go on the new Mercedes-Benz E-Class to be launched next year.
“By the year 2020, the automotive market is expected to grow to 100 million new vehicles per year. The trend of lightweighting in transport industry has become a major theme of research in recent years, the main goals being anticipated fuel savings and meeting stricter environmental legislations in various jurisdictions such as Europe, North America, and Asia. This has led to component manufacturers across the world to come up with lightweight solutions for their OEM customers,” says Gajanan Gandhe, executive director, India and VP, South Asia & Africa.
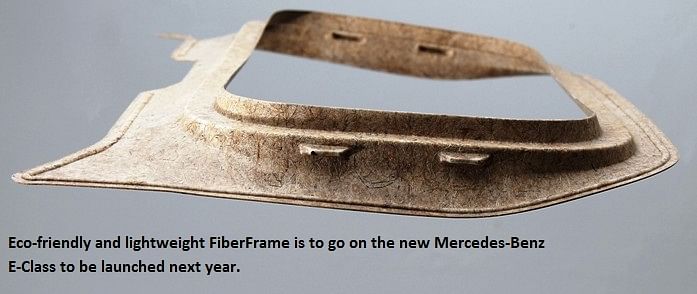
“IAC embraces and deploys continuous improvement philosophies and shares best practices globally including India. Fuelled with a passion to deliver exciting solutions, IAC has recently developed new products that are innovative, lighter in weight and environmental friendly interior solutions. IAC’s processes and products help reduce environmental impact with recyclable materials, supporting efficient manufacturing.”
Over the years, apart from lightweight metallic alloys and multi-material design options, according to Jayan, emerging trends in fibre-based hybrid composite structures have provided viable solutions in the development of lightweight vehicles.
“Recent technological advances in the utilisation of cellulose and carbon fibre-enabled composite formulations have led to revolutionising of the design of not only standard but also luxury vehicles,” he points out.
Jayan believes that due to their favorable strength-to- weight ratios, plastics are now accounting for almost 50 percent of the volume of vehicles currently. “However, they account for only about 10 percent of the overall vehicle weight. The main goal is the reduction of mass of motor cars. The order of the day is that technology has to reduce the weight of the vehicles, and the move would be towards using more plastic components as well as aluminum to help in weight reduction. And with increased awareness towards cleaner environment, better utilisation of existing resources and stringent emission norms, we shall continue to see an upward trend in terms of usage of plastics and other lightweight materials in the years to come,” he foresees.
INTERVIEW Gajanan Gandhe, executive director — India & vice-president, South Asia, Africa, IAC
How do Indian OEMs view the increasing role of plastics and polymers in replacing metals in a vehicle’s anatomy?
The Indian automotive market, which has witnessed a turnaround in the past year, is showing signs of positive growth continuing for the next 3-5 years. This is also driven by the large-scale investments made by the government of India in the infrastructure sector and reduction of interest rates while controlling inflation.
With the decision to move to BS VI emission norms by 2020 and stringent regulations for a cleaner environment, Indian OEMs therefore are encouraged to use more of lighter weight alternatives so they can reduce the cost as well as the price of their vehicles.
The use of plastics to replace metal components in cars in India is, therefore, slated to rise in double digits in the coming three to four years, riding mainly on the initiatives taken by original equipment manufacturers to reduce weight of the vehicles. Currently, the engineering plastics industry roughly grows at twice the auto industry's production in the country.
Do you think lightweighting efforts will be impacted by the decision to move to BS VI emission norms by 2020? If yes, how?
The decision by the Indian government to pull ahead the implementation of BS VI compliance for all passenger vehicles by 2020 definitely has affected the entire planning and development of new vehicles, making a lot of products and technologies obsolete while shifting the focus to new technologies that are compliant with these standards. At the same time, carmakers and suppliers have to continue producing spare parts for the vehicles that are already on the road, which requires a significant amount of planning, storage and inventory management, leading to an increase in the cost of these spares.
However, fuelled with a passion to deliver exciting solutions all the time, a company like IAC shall continue to work towards bringing new innovative products that are lighter in weight and environmental- friendly interior solutions. Sustainability is paramount in all that IAC does. IAC’s processes and products help reduce environmental impact with recyclable materials, supporting efficient manufacturing. We continue to work towards lightweighting and fuel efficiency without getting affected by government emission norms.
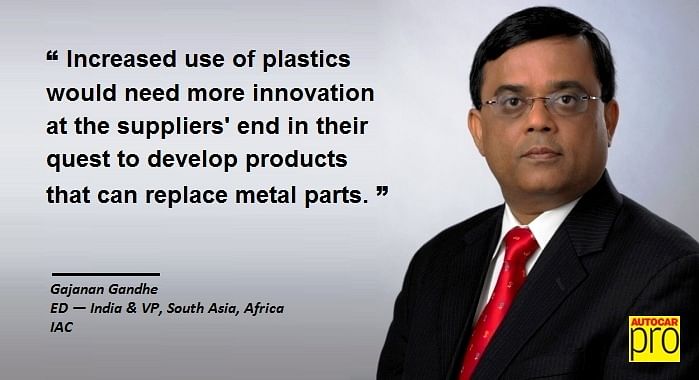
It is understood that BS VI engine technologies (SCR/ EGR / DPFs) will result in weight gains in the drivetrain area and the average vehicle weight will grow upwards. How can OEMs and suppliers counter this challenge? Are OEMs notifying polymer part suppliers to relook at further reducing the weight of components?
There is a constant demand and pressure from the OEMs to look at lighter alternatives for reducing the weight of components. The use of plastics is likely to grow as OEMs bid to reduce prices as well as look at reducing costs. However, this would need more innovation at the suppliers’ end as they look to develop products that can replace metal parts.
Can you detail a few product examples where IAC has managed to cut component weight and also the technology used?
IAC has recently started producing its unique, lightweight injection moulded inner dash insulation for superior interior acoustical performance for two premium European OEM customers at its new Prestice 2 production facility in Prestice, Czech Republic.
IAC’s industry-leading injection moulded dash inner provides an estimated 40 percent weight reduction compared to a conventional vacuum-formed product. The IAC injection moulding process provides exact, reliable, forming of lighter inner dash insulation without compromising acoustic performance and also delivers better mass distribution to match the acoustic hotspots within the component.
Within its vertically integrated approach, IAC has also developed a customised injection moulding resin to fulfill the high quality requirements of these two premium customers.
Injection moulded dash inner insulation complements IAC’s offer of lightweight acoustical insulation products, which also includes the industry first sprayed polyurethane (PUR) inner dash technology.
PUR-sprayed inner dash insulation with back foaming achieves weight reductions of about 20 percent, coupled with a superior acoustic performance. For the past few years, PUR-sprayed dash inner insulation has been in production at IAC Spartanburg, South Carolina, USA and IAC Straubing, Germany, where it recently debuted on the new luxury Maserati Levante sports utility vehicle.
RELATED ARTICLES
Tata Motors: From Ice Legacy To Electric Intelligence
Tata Motors has a lot riding on the newly launched Harrier EV, coming as it does on a fresh, EV-oriented software platfo...
Complete List of Cars and SUVs Tested by Bharat NCAP
Bharat NCAP has crash-tested 20 models to date, including both ICE-powered vehicles and EVs.
Belrise Industries: A Story of Grit and Focus
The Belrise Industries IPO is the culmination of a multi-decade journey by entrepreneur Shrikant Badve that started in a...