‘We are working on a product for an OE customer that could very well come to India.’
Professor Gordon Murray speaks to Sumantra B Barooah about iStream, his ‘disruptive’ manufacturing technology, the T25 and other mobility concepts, India’s engineering strengths and his mobility concept for India.
Professor Gordon Murray speaks to Sumantra B Barooah about iStream, his ‘disruptive’ manufacturing technology, the T25 and other mobility concepts, India’s engineering strengths and his mobility concept for India.
First, as an engineer, what comes to your mind when you’re here in India?
What comes across to me, as an engineer, is the difference in the kind of problems you have here and elsewhere in the world. The basic problems are the same but the difference lies in how we go about solving problems. For example, the traffic flow issues. India has a massive concentration of two-wheelers, something I have not seen anywhere else on the planet. That leads to a set of urban planning issues that we don’t see in Europe.
I’d like to have a crack at the problem from a congestion point of view because the vehicle footprints aren’t what you’d expect. You’ve got the little autorickshaws that are fine because the density of occupants is very good. But there are cars where occupant density is low. Rather than look at it from a car design perspective, I’d like to look at the Indian traffic congestion problem from an urban traffic flow viewpoint.
So would products like the T25 or T27 be suitable for India?
Definitely in urban areas. It’s not just the footprint, it’s about fuel economy and emissions. The T25 has a four-star Euro NCAP rating, so it’s a safe, small package and good for an urban environment. You are doing no damage and not causing congestion because you have a
small footprint. It’s three people in a tiny little motor car.
Would you like to have a T25 derivative tailor-made for emerging markets?
In its base form, it’s perfect because it will be very low cost, way below the segment the Yamaha Motiv is designed for.
You won’t be surprised if Yamaha with its Motiv has India in its sights, would you?
Yamaha is concentrating on Europe for now but it does have aspirations I’m sure. I think it wants to see how the Motiv does in Europe.
Your iStream concept is a very radical way of manufacturing. Why haven’t four-wheeler OEMs taken to it so far?
It has taken a while but they are. Before 2008, when the energy crisis and the financial collapse occurred almost simultaneously, we thought we’d never see an OE with iStream. It’s just too disruptive. OEs have invested huge sums in metal, stamping and they have an enormous amount of knowledge in stamp metal. iStream doesn’t use any of that stuff.
I didn’t think they’d be interested at all but the coincidence we had has been lucky for us as far as timing goes. It brought a lot of OEs to our door. We are now working with four customers on six motor cars. There are many reasons for this if you think about it. There’s uncertainty with future powertrains.
Then, there’s a need to reduce weight for efficiency and there’s a limit as to how much weight you can reduce with steel and anything else you try to reduce, you spend money. With iStream, one spends less money to save weight, so it’s attractive.
There’s a massive change in the way young people are looking at car ownership – purchasing models, ownership models, servicing models. The old model of investing millions or billions in a platform for 10 with a couple of facelifts and making around 200,000 cars a year and making a return on investment in year six or seven… it just doesn’t work, I think, anymore.
What are the advantages of iStream over conventional manufacturing?
The savings for iStream come in different areas. The first is in capital investment. We can reduce that by 80 percent but the figure may vary. The best case we’ve seen is an 85 percent reduction.
Secondary savings come in manufacturing energy. The factory is much smaller. The frame plant is only about 17-20 percent the size of a standstill plant, so we use 60 percent less energy. Then the real savings come for the end user, a stronger but lighter car that uses less fuel.
What is the optimum production level for which the iStream technology would be ideal?
From a volume point of view, it works pretty well down to about 15,000-20,000 units. Actually you can de-mechaniseiStream. The manufacturing process for the bodyshell, the monocoque, is normally about 95 percent automated. If you de-automated that, one could go down below 15,000 on the bottom-end and the top-end is about 150,000-160,000 annually. The sweet spot’s around 80,000-100,000 units a year.
Has any Indian OE expressed an interest?
One of our customers is from this part of the world but the product isn’t for this region at the moment. We are actually working on another product for an OE customer that could very well come to India.
What is your opinion about engineering capabilities in India here and what’s your take on frugal engineering?
In my view, one company that’s impressive is Tata Motors. One has to look at what the company has done over the last decade, not in commercial vehicles, which is successful but from a passenger cars standpoint, what the Tata Group has done with Jaguar Land Rover is a success story.
I didn’t think I could see something like that in England. In India, to have the foresight to try and make the Nano as a complete rethink on low cost is another achievement.
So if you look at what Tata has done at two exceptional extremes, JLR, it is difficult to think of another brand they could have picked – it was a prestigious brand that needed saving. BMW and Mercedes didn’t need saving. Tata has done a massive turnaround.
Then you go right to the other end of the scale and try and build a car for a thousand pounds (Rs 100,000). I know it didn’t quite work out to that much. But the vision to do that – in some cases the vision is more important than the actual result.
You can point a finger at me and say I made 100 cars for rich people but it’s inspired a lot of people to think and hope from its engineering and vision, and you can say the same thing about the Nano. I’m sure a lot of OEMs got a big fright when it was announced and worked more on reducing the cost for the end customer. I can’t think of another car company that has said that it’s done that.
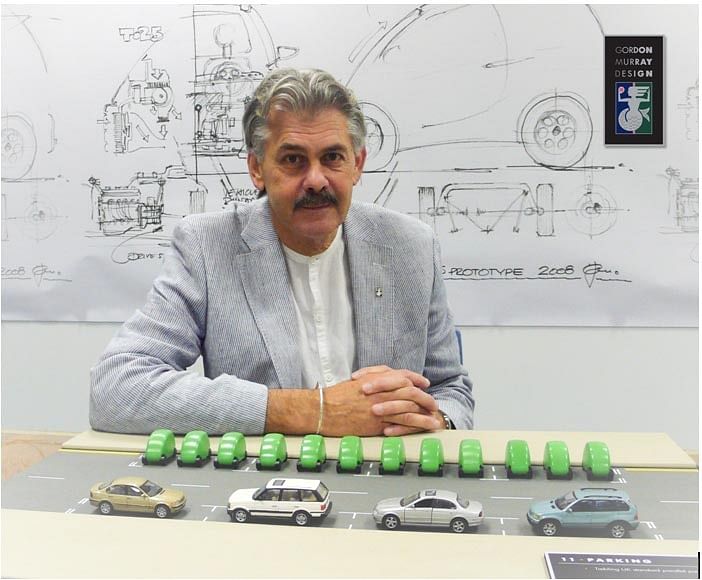
You have translated a lot of tech from Formula 1 into your manufacturing. Do you think there are more things that can go into road cars? If yes, what could they be?
I think there are technologies in Formula 1 that influence road cars. The obvious ones are fuel and tyre design, basic advances in engines, clutches, electronic control systems. Probably not for aerodynamics because F1 cars are made specifically for downforce. The difficult one has been materials.
The McLaren F1 wasn’t a clever car at all. I only took handmade F1 technology and made a very expensive road car with the same technology. That’s not clever – it’s just transferring technology from one area to the other. iStream, on the other hand, is very clever because that takes F1 and reduces the cycle production time and cost, affordable by anyone here. So, that’s the trick. It doesn’t use F1 materials, but it uses F1 tech.
Sometimes what is transferred from F1 is inspirational only, sometimes it’s functional, sometimes it’s a system crossover, not using materials. There’s carbon fibre, a big thing in the car industry. It’s supposed to get as cheap as chips very soon. It’s not. It’s very expensive. You can use it for small sections like BMW is doing. But to make a complete carbonfibre road car would never be affordable for the everyday motorist like you and me.
You’ve mentioned that you’ve got as many as seven new ongoing projects. What is the range of applications we may see?
It’s incredibly broad. On the small end, there’s a two-seater city car, it doesn’t get smaller than that. And at the other end, we’re working on a 3.5-tonne off-road truck, which is iStream. And everything in between.
Three years ago, we were in great danger of becoming known as a city car company because that’s what we started with, with the 25 and 27. But it couldn’t be further from the truth. We’re working on a whole range of vehicles, of different sizes.
You’re a strong proponent of lightweighting technologies. Can you tell us in what ways can the envelope be pushed in this area?
At present, the big problem is that in the auto industry, people are focussing on tiny parts of the car, which don’t give you a step change. Making a carbonfibre boot, or bonnet or door skin isn’t going to get the job done, it really isn’t. It is expensive.
I think the only way we’re going to make a step change is to do something like we’re
doing, which is very disruptive, where you take the whole structure of the motor car, chuck out the whole lot and start again. That’s iStream.
So there would be many more concepts focussed on reducing weight from you?
We don’t stop. Everything is patented and that’s not even the real protection. We’re already working on iStream 1.5, 2 and iStream 3. A lot of different materials using the same technology.
Are you working on any new ways to improve the efficiency of the IC engine?
We have a powertrain department and we’re working on hybrids, petrols, diesel. We built a hydrogen fuel cell for one customer but we’re not really engine people. We have a powertrain department as a service industry to iStream, which is our core product. But I think there are some advances still to come and probably on downsized engines with forced induction. So, combining turbocharging and supercharging and variable turbocharging. There may be some biggish steps but no one major step, it’ll be lots of small steps.
Trouble is, it’s the law of diminishing returns again. A bit like materials and car structure. It’s more expensive, every time you have variable valve timing, twin spark plugs, every single time. Without a doubt, the last frontier where we can make a big step forward is weight.
So, when’s the next big step from Gordon Murray Design?
I would like to get one of our cars into production so people can experience it. It’s not about fuel consumption and emissions. It’s all about driving pleasure. I’d like a very rigid, lightweight car with independent suspension that will be a lot more fun todrive, at any speed.
Have you looked at tapping India’s talent pool?
We actually have three to four staff members from India. That is decent considering our entire workforce is 65-strong.
At a later stage, could we see some sort of a satellite centre in India?
It could happen. In fact, right now we’re working with the Brazilian government to set up a technology centre with the Rio University. So, it’s a possibility.
RELATED ARTICLES
India: A Bastion Of Stability for Schaeffler
German autoparts maker Schaeffler’s CEO, Klaus Rosenfeld, describes India’s role in the company’s €24-25 billion empire....
'No Question of Us Being Late' - Suzuki India on e-2Wheeler Market
Suzuki Motorcycle India believes its EV entry is timely as the market is now mature enough to grow off genuine demand ra...
'India Can Become a Major Pillar for Us' - Marquardt Group
Björn Twiehaus, CEO of Marquardt Group, and Vishal Narvekar, the company's India GM, share their outlook on the Indian m...